Adjusto-Spede Motor Repair Services in Michigan
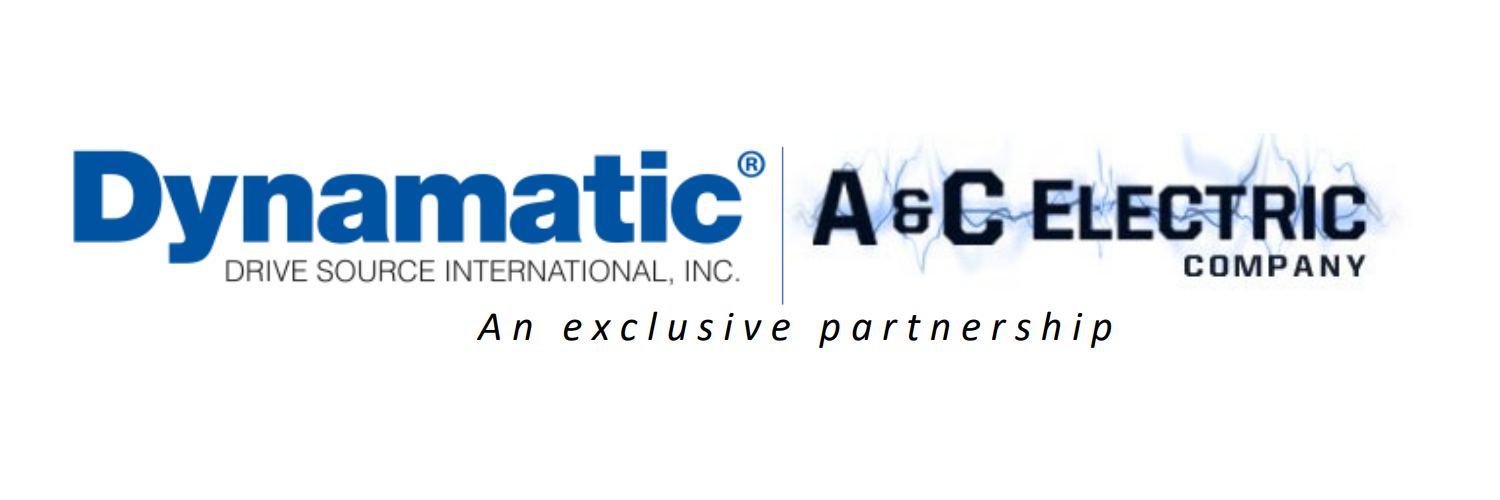
A&C Electric provides Adjusto-Spede motor repair to companies in Michigan, Indiana and Ohio. We work with DSI Dynamatic, Eaton and Louis Allis drives, offering quick diagnostics and in-house service capabilities for every model. Contact us today for a quote on Adjusto-Spede motors across the Midwest.
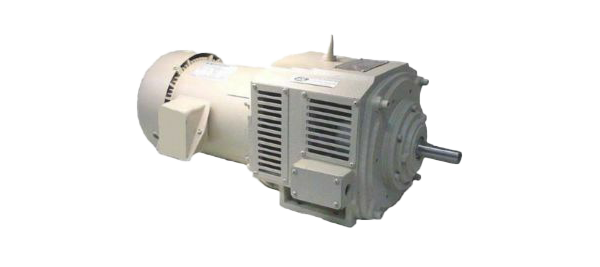
How Adjusto-Spede Drives Work
Adjusto-Spede Drives use an air-cooled, adjustable speed clutch paired with a NEMA B AC induction motor to deliver constant torque across a variable speed range. There’s no physical contact between input and output, which helps reduce wear and extend motor life.
Each drive includes:
- TEFC construction and C-Face endbells
- Internal tachometer generator for real-time feedback
- DC excitation to the clutch coil via the controller
Speed is regulated by comparing the tachometer signal to a reference point within the controller. This feedback loop produces smooth response with reduced shock loading—ideal for high-inertia loads and precision industrial motor control.
Adjusto-Spede systems deliver a 34:1 speed range at 250% rated torque, making them ideal for high-load startups. Because Adjusto-Spede drives differ significantly from standard motor types, they require specialized knowledge and equipment. A&C Electric technicians have decades of experience repairing industrial electric motors and strive to save customers money by reducing lead time and spare motor costs.
Variable Speed Drive Models We Service
-
AS & FAS Drives: Smooth, Compact Speed Control
Dynamatic AS and FAS drives offer tight speed control with simple drop-in installation, especially in fractional horsepower ranges.
- Available in 1/4 to 1.5 HP units
- Compatible with single or three-phase power
- 34:1 speed range and 250% rated motor torque
- Built with permanently lubricated bearings and C-face mounts
- Matches overload requirements and existing wiring
- No special training or wiring changes required
-
AT Drives: Built for Stamping Presses
Originally engineered for press applications, AT drives provide rugged performance and consistent torque under changing loads.
- 1–200 HP capacity with tachometer feedback
- Speed control within 0.5% from no load to full load
- 250% rated torque for high-inertia startups
- Minimal harmonics with low-maintenance design
- Small controller footprint with PLC compatibility
- Used in presses, kilns, bitumen pumps and cold feed bins
-
DCD Drives: Low-Maintenance in Harsh Conditions
DCD drives combine durability with simplicity for demanding environments like mining and asphalt processing.
- Air-cooled, adjustable speed clutch with AC induction motor
- Self-cleaning rotor for dust and debris resistance
- 250% startup torque and consistent speed regulation
- TEFC design with no routine maintenance
- Drop-in NEMA and IEC motor frame compatibility
- Reliable performance in conveyor and aggregate systems
Our team repairs and refurbishes Adjusto-Spede industrial motors using precision tools, proper handling techniques and decades of hands-on experience. Each motor is returned quickly and at a significantly lower cost than replacement.
AS Motor Repairs
- AS-140104-0145
- AS-140104-0190
- AS-140106-0145
- AS-140106-0190
- AS-140154-0145
- AS-140154-0190
- AS-140204-0145
- AS-140204-0190
- AS-140304-0145
- AS-140304-0190
- AS-180156-0145
- AS-180156-0190
- AS-180206-0145
- AS-180206-0190
- AS-180304-0145
- AS-180304-0190
- AS-180306-0145
- AS-180306-0190
- AS-180504-0145
- AS-180504-0190
- AS-210506-0145
- AS-210506-0190
- AS-210754-0145
- AS-210754-0190
- AS-211004-0145
- AS-211004-0190
- AS-250756-0145
- AS-250756-0190
- AS-251006-0145
- AS-251006-0190
- AS-251504-0145
- AS-251504-0190
- AS-252004-0145
- AS-252004-0190
- AS-271506-0145
- AS-271506-0190
- AS-272004-0145
- AS-272004-0190
- AS-272006-0145
- AS-272006-0190
- AS-272504-0145
- AS-272504-0190
- AS-272506-0145
- AS-272506-0190
- AS-273004-0145
- AS-273004-0190
- AS-274004-0145
- AS-274004-0190
- FD-2541-4001
- FD-2541-4002
- FD-2543-4001
- FD-2543-4002
- FD-5021-4001
- FD-5021-4002
- FD-5023-4001
- FD-5023-4002
- FD-5041-4001
- FD-5041-4002
- FD-5043-4001
- FD-5043-4002
- FD-7521-4001
- FD-7521-4002
- FD-7523-4001
- FD-7523-4002
- FD-7541-4001
- FD-7541-4002
- FD-7543-4001
- FD-7543-4002
- FD-9523-4001
- FD-9523-4002
- FD-9923-4001
- FD-9923-4002
- FD-9941-4001
- FD-9943-4001
- FD-9943-4002
AT Motor Repairs
- AT-140014-0145
- AT-140014-0190
- AT-140024-0145
- AT-140024-0190
- AT-180034-0145
- AT-180034-0190
- AT-180054-0145
- AT-180054-0190
- AT-180074-0145
- AT-180074-0190
- AT-210074-0145
- AT-210074-0190
- AT-210104-0145
- AT-210104-0190
- AT-210154-0145
- AT-210154-0190
- AT-250154-0145
- AT-250154-0190
- AT-250204-0145
- AT-250204-0190
- AT-250254-0145
- AT-250254-0190
- AT-280254-0145
- AT-280254-0190
- AT-280304-0145
- AT-280304-0190
- AT-280404-0145
- AT-280404-0190
- AT-280504-0145
- AT-280504-0190
- AT-320256-0145
- AT-320256-0190
- AT-320304-0145
- AT-320304-0190
- AT-320306-0145
- AT-320306-0190
- AT-320404-0145
- AT-320404-0190
- AT-320406-0145
- AT-320406-0190
- AT-320504-0145
- AT-320504-0190
- AT-320604-0145
- AT-320604-0190
- AT-320754-0145
- AT-320754-0190
- AT-360506-0145
- AT-360506-0190
- AT-360604-0145
- AT-360604-0190
- AT-360606-0145
- AT-360606-0190
- AT-360754-0145
- AT-360754-0190
- AT-361004-0145
- AT-361004-0190
- AT-361254-0145
- AT-361254-0190
- AT-440756-0145
- AT-440756-0190
- AT-441004-0145
- AT-441004-0190
- AT-441006-0145
- AT-441006-0190
- AT-441254-0190
- AT-441256-0145
- AT-441256-0190
- AT-441504-0145
- AT-441504-0190
- AT-442004-0145
- AT-442004-0190
DCD Motor Repairs
- DCD-132030-4141
- DCD-132050-4121
- DCD-132050-4141
- DCD-132075-4121
- DCD-132100-4121
- DCD-160075-4141
- DCD-160100-4141
- DCD-160150-4121
- DCD-160150-4141
- DCD-160200-4121
- DCD-160250-4121
- DCD-180150-4141
- DCD-180200-4141
- DCD-180250-4121
- DCD-180250-4141
- DCD-180300-4121
- DCD-180300-4141
- DCD-225300-4141
- DCD-225400-4141
- DCD-225500-4141
- DCD-225600-4141
- DCD-225750-4141
Contact A&C Electric for expert Adjusto-Spede repair in Michigan and surrounding states.


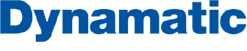